Фильтр Пресс Инструкция
Фильтр-прессы для отжима винограда, яблок и фруктов. Ленточные камерные рамные пресс. Перед использованием фильтр-пресса, внимательно ознакомьтесь с инструкцией по технике безопасности при работе с прессовым оборудованием и с инструкцией по эксплуатации. 1.3.Лица, допускающие нарушения требований инструкций по охране труда, привлекаются к ответственности согласно «Закона об охране - исправность манометров на фильтр-прессах.
Вспомогательное оборудование в схемах вакуумных фильтровальных установок В схемах фильтровальных установок используется следующее вспомогательное оборудование: ресиверы, гидравлические ловушки, вакуум-насосы, воздуходувки, клапаны и др. Ресиверы используют для разделения водовоздушной смеси на жидкость и воздух. Применяются ресиверы с радиальным и тангенциальным вводами разделяемой смеси. Радиальный ресивер представляет собой цилиндрический резервуар со сферическими крышками и днищами с патрубками ввода смеси, отвода воздуха и фильтрата. Внутри установлен отбойник. Имеется смотровой люк.
Попадая в ресивер, поток водовоздушной смеси резко снижает скорость вследствие расширения объема, а также изменения направления движения. Наталкиваясь на установленный в ресивере отбойник-перегородку, газожидкостный поток разделяется: жидкость стекает вниз, а очищенный воздух устремляется вверх.
В последнее время все более широкое применение находят ресиверы с тангенциальным вводом водовоздушной смеси, разделение которой происходит в поле центробежных сил. Для создания разрежения применяются поршневые или водокольцевые вакуум-насосы. Поршневые насосы (обычно ВН-120М) применяются на многих действующих горно-обогатительных комбинатах. Как показала практика, для поршневых насосов требуется тщательная очистка отсасываемого воздуха от воды и твердых частиц во избежание быстрого износа клапанов, колец и пр. Однако эти насосы обладают высоким к.п.д. (до 85%) и пониженной энергоемкостью. Поршневые насосы представляют собой одноступенчатые одноцилиндровые горизонтальные машины двойного действия, создающие разрежение до 100 кПа.
Водокольцевые вакуум-насосы ВВН-300 нашли применение на горно-обогатительных комбинатах большой производительности. Они не нуждаются в высокой степени очистки воздуха; кроме того в рабочей полости этих машин нет трущихся деталей, что обеспечивает их большую долговечность.
Насос состоит из частично заполненного водой корпуса, в котором эксцентрично расположено рабочее колесо с изогнутыми лопатками. Недостаток водокольцевых насосов – их низкий коэффициент полезного действия, составляющий 35%. Для создания давления воздуха при отдувке осадка в отделениях фильтрования широкое применение находят водокольцевые воздуходувки и турбовоздуходувки. Конструктивно водокольцевые воздуходувки типов ВВН и ГРМК не отличаются от водокольцевых вакуум-насосов, но комплектуются более мощными электродвигателями.
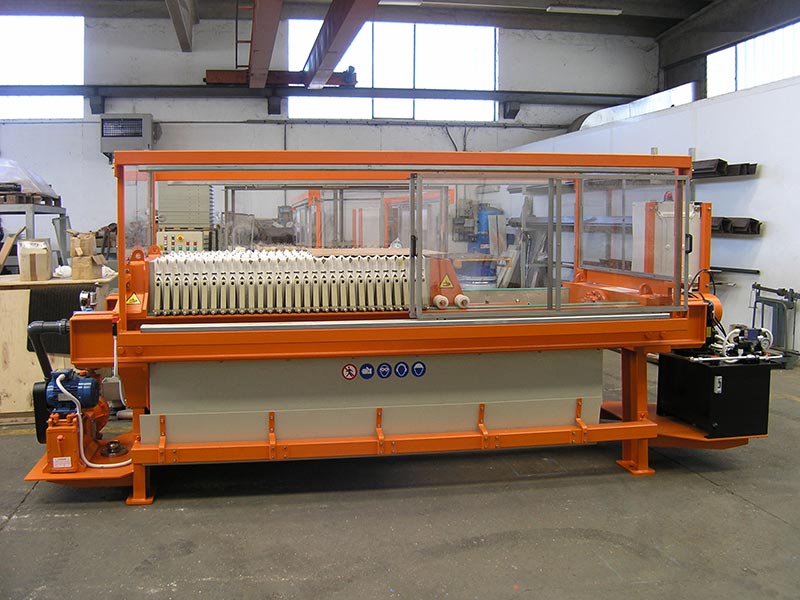
Турбовоздуходувки значительно производительней водокольцевых воздуходувок и потребляют меньше энергии на 1 м 3 воздуха. Подача их достигает 200 м 3/мин. Поэтому они рекомендуются к применению на фабриках высокой производительности. Для предохранения вакуум-насосов от возможного попадания в них жидкости и конденсирующихся паров из ресивера, а также на случай аварийного состояния системы удаления фильтрата, применяют барометрические конденсаторы, называемые ловушками. Ловушку устанавливают между ресивером и вакуум-насосом выше ресивера.
Внутри ловушки имеется отбойник-перегородка. Ловушка соединяется одной трубой с ресивером через его крышку, а другой трубой с вакуум-проводом, идущим к вакуум-насосу.
Для стекания остатков фильтрата служит барометрическая труба длиной 10 м. Гидрозатвор представляет собой приемник прямоугольного сечения объемом примерно 1 м 3, заполненный водой, в которую опущена барометрическая труба. Фильтрат из гидрозатвора переливается в зумпф, откуда насосами перекачивается в определенное место технологической схемы фабрики. Во избежание заиливания гидрозатвора частицами твердого к нему подводится свежая вода для периодической промывки днища. Характеристики основного и вспомогательного оборудования в отделениях фильтрования горно-обогатительных комбинатов приведены в литературе 5. Фильтрование под действием избыточного давления применяется для труднофильтруемых пульп с тонкодисперсными частицами в тех случаях, когда вакуум-фильтры не дают хороших результатов. Главным преимуществом использования напорных фильтров является то, что достигается более высокая разность давлений по обеим сторонам фильтрующей перегородки (движущая сила фильтрования), в результате чего повышается степень фильтрации и снижается конечная влажность продукта.
Давление в фильтр-прессах может достигать 2 МПа и, следовательно, эти фильтры могут быть использованы для получения кека с высоким удельным сопротивлением. На зарубежных обогатительных фабриках фильтр-прессы получили значительное распространение, поскольку позволяют получать осадок минимальной влажности. Их применяют на углеобогатительных фабриках, на гидрометаллургических заводах, при обезвоживании каолиновых, тальковых суспензий, а в последние годы достаточно широко для обезвоживания концентратов цветных металлов (медные, цинковые, свинцовые, оловянные, никелевые, кобальтовые концентраты), шламов.
Фильтр-прессы как аппараты, допускающие большой перепад давлений, обладают высокими показателями обезвоживания и чистоты фильтрата. По характеру работы фильтр-прессы подразделяются на аппараты периодического и непрерывного действия. По направлению перемещения фильтровальных плит подразделяются на горизонтальные и вертикальные фильтр-прессы. В зависимости от устройства фильтровальных камер различают горизонтальные, рамные, камерные, диафрагмовые (мембранные), а также непрерывно действующие ленточные фильтр-прессы. В зарубежной практике для обезвоживания тонкоизмельченных продуктов крупностью менее 30–40 мкм используются трубчатые фильтр-прессы, в которых давление фильтрования достигает 1410 5 Па.
Принцип работы всех фильтр-прессов при всем многообразии конструкций одинаков. В фильтр-прессах фильтрование происходит в вертикальных или горизонтальных камерах, образуемых фильтровальными плитами, перфорированные, ребристые или рифленные стенки которых обтянуты фильтротканью. При сжатии плит в образующиеся камеры подают пульпу под давлением до полного заполнения камер, при этом жидкая фаза “отжимается” через фильтроткань и на ней формируется осадок. Во многих конструкциях фильтр-прессов предусмотрено диафрагменное сжатие осадка при подаче воды под давлением или сжатого воздуха в пространство над резиновой диафрагмой, установленной на одной из стенок камер. При необходимости осуществляется продувка осадка сжатым воздухом, а при разжиме плит происходит разгрузка осадка. В более ранней ручной конструкции фильтр-прессы требовали интенсивного труда. Современные фильтр-прессы полностью автоматизированные.
Горизонтальные фильтр-прессы благодаря вертикальному расположению плит отличаются развитой фильтрующей поверхностью, относительно простой конструкцией и могут быть полностью механизированы и автоматизированы. Горизонтальный фильтр-пресс (рис. 4.22) состоит набора вертикально расположенных фильтровальных плит 1, размещенных между концевыми плитами: неподвижной упорной 2 и подвижной натяжной 4. Подвижные плиты экипированы фильтровальной перегородкой. При сжатии плит образуются камеры с каналами подачи фильтруемой суспензии, сжатого воздуха, промывной жидкости и отвода фильтрата. Схема устройства горизонтального фильтр-пресса Фильтровальные плиты передвигаются на двух параллельно расположенных стяжных штангах 3, закрепленных в упорной плите 2 и в стойке 6 зажимного устройства 5.
Усилия, возникающие при фильтровании под давлением, воспринимают концевые плиты 2 и 4. Фильтр работает следующим образом. После зажима плит в образованные ими камеры под давлением подается суспензия. При полном заполнении камер на фильтровальной ткани формируется осадок. Фильтрат отводится по каналам наружу. Процесс фильтрования осадка продолжается до полного заполнения им всего объема камер. Затем при необходимости производится промывка и просушка его сжатым воздухом.
После просушки осадка отодвигается нажимная плита, промежуточные плиты разжимаются поочередно. Осадок разгружается, после чего цикл повторяется. Схемы устройства рамного (а), камерного (б) и диафрагмового (в) фильтр-прессов В рамных фильтр-прессах (рис. 4.23, а) осадок накапливается в пространстве между чередующимися плитами 1 и рамами 2.
Фильтровальные плиты, экипированные фильтротканью, имеют дренажную поверхность. Для выхода фильтрата в них предусмотрены отверстия. Плиты и полые рамы расположены между опорной 3 и нажимной 4 плитами.
Последовательность операций обезвоживания следующая: фильтрование, промывка, просушка, разжим плит, выгрузка осадка. В камерных фильтр-прессах (рис.
4.23, б) осадок накапливается в камерах, образующихся между двумя соседними плитами вследствие имеющихся в них углублений. Камерный фильтр-пресс состоит из фильтровальных плит 1 одинаковой конструкции, между которыми в два слоя 2 и 3 уложена фильтровальная ткань.
При сближении плит она служит уплотнением образующихся камер. По каналу 5 подается фильтруемая суспензия. Фильтрат собирается на рифленой поверхности плит и удаляется по каналам 4 и 6. Жидкость для промывки подается по каналу 5. Последовательность операций обезвоживания на камерном фильтре аналогична рамному. Мембранные или диафрагмовые фильтр-прессы для отжима осадка снабжены эластичными (резиновыми или резинотканевыми) мембранами или диафрагмами.
Обезвоживание осадка осуществляется под давлением воды или воздуха, подаваемыми под диафрагмы. Схема одной из разновидностей мембранного фильтр-пресса показана на рис. Между фильтровальными плитами, экипированными фильтротканью 3, расположены отжимные плиты 2, снабженные диафрагмами 4.
Фильтровальные и отжимные плиты находятся между нажимной 7 и упорной 9 плитами, суспензия подается по каналу 8, сжатый воздух – по каналу 6. Фильтрат отводится через отверстия в перфорированных листах 5 и каналы 10. Применение диафрагм позволяет сформировать осадок равномерной толщины, сократить расход сжатого воздуха, снизить влажность осадка.
Наиболее целесообразно использование мембранных фильтр-прессов при обезвоживании сжимаемых осадков. Заводом «Прогресс» серийно выпускаются: рамный фильтр-пресс ФПГ-140 с общей площадью фильтрования 140 м 2, ФРАМ‑200 с общей площадью фильтрования 200 м 2, камерный диафрагмовый фильтр-пресс ФПАВ-300 с площадью фильтрования 300 м 2, камерный бездиафрагмовый фильтр-пресс ФКМ-600 с площадью фильтрования 600 м 2. Заводом «Прогресс» изготавливаются фильтр-прессы ФКМ с верхней подвеской плит на базе европейских плит LENSER: размером 1200´1200 мм (типоразмерный ряд 25–160 м 2) и 1500´1500 мм (100–500 м 2). Условное обозначение: Ф – фильтр-пресс, К – камерный с вертикальными плитами, М – механизированный зажим. Фильтр-пресс состоит из комплекта фильтровальных плит, подвешенных с помощью специальных кронштейнов на верхней балке (включающей в себя механизм перемещения плит), нажимной плиты, передней и задней опор, механизма зажима (электромеханического или гидравлического), устройства для регенерации фильтроткани, гидроуправляемых поддона и технологической запорной арматуры.
Суспензия через центральный коллектор подается в фильтровальные камеры сжатого комплекта плит. Жидкая фаза проходит через фильтрующую салфетку и отводится в коллектор. При необходимости возможна промывка осадка. По окончании цикла фильтрования подается воздух для просушки осадка. Осадок из межплиточного пространства саморазгружается в процессе перемещения плит к отодвинутой нажимной плите.
Толщина осадка 30 мм. Отличительными особенностями фильтр-прессов ФКМ являются: высокое рабочее давление (до 1,5 МПа) обеспечивает фильтрацию труднофильтруемых суспензий и значительно более высокую производительность; полипропиленовые плиты более долговечны и дают возможность работы с агрессивными средами; верхняя подвеска плит позволяет снизить энергозатраты и обеспечивает высокую скорость выгрузки осадка; проще в техническом обслуживании и ремонте; не нуждаются в специальном фундаменте. Вертикальные фильтр-прессы. Наиболее распространенными являются автоматические камерные фильтр-прессы типа ФПАКМ, выпускаемые Бердичевским заводом «Прогресс». Камерный автоматический фильтр-пресс типа ФПАК (рис. 4.24) состоит из верхней упорной 10, нижней нажимной 13 и ряда параллельных, горизонтально расположенных, фильтровальных плит 12, между которыми проходит бесконечная лента фильтроткани 6, огибающая ролики 4, где происходит съем осадка с нее ножами 5 в приемники. Натяжение фильтроткани производится с помощью устройства 7, промывка ее и зачистка скребками – в камере регенерации 2.
Вертикальный фильтр-пресс ФПАКМ: 1 – конвейер; 2 – камера регенерации; 3 – привод передвижения ткани; 4 – ролики; 5 – ножи съема осадка; 6 – фильтровальная ткань; 7 – натяжное устройство; 8 – коллектор подачи; 9 – коллектор отвода; 10 – верхняя упорная плита; 11 – стяжки; 12 – фильтровальные плиты; 13 – нижняя нажимная плита; 14 – электромеханический зажим; 15 – рама Фильтровальные плиты могут передвигаться вверх и вниз вдоль плоских стяжек 11, которые служат направляющими для роликов плит. Зазор между плитами при их опускании 45 мм. Между плитами зигзагообразно в виде бесконечной ленты протянута фильтровальная ткань. Ткань приводится в движение приводным барабаном и прижимными роликами, установленными на прижимной плите. Кек разгружается на обе стороны фильтра. После выхода из межплиточного пространства ткань проходит камеру регенерации и роликовые приспособления, поступая снова в межплиточное пространство. При сжатии плиты образуют два коллектора, из которых один 8 служит для подачи исходной пульпы, промывной воды, сжатого воздуха, второй 9 – для отвода фильтрата, промывной воды и воздуха.
Установка опирается на раму. Фильтр-прессы ФПАКМ изготовляют в двух исполнениях: с диафрагмами для отжима и без диафрагм с просушкой осадка воздухом. Фильтровальная плита (рис. 4.25) состоит из верхней и нижней рам. Верхняя рама перекрывается перфорированным листом, покрытым фильтротканью, и является камерой для отвода фильтрата. Нижняя рама при сжатии плит служит камерой фильтрования.
Под днищем нижней рамы закреплена эластичная диафрагма, на которую подают воду под давлением 1,17 МПа для отжатия влаги из осадка. Поперечный разрез фильтровальных плит: 1 – верхняя рама; 2 – перфорированный лист; 3 – фильтроткань; 4 – нижняя рама; 5 – диафрагма Фильтр-пресс работает периодически. Цикл фильтрования состоит из следующих основных операций: 1. При помощи электромеханического зажима фильтровальные плиты сжимаются вместе с фильтротканью с одновременным гидравлическим уплотнением образующихся камер.
Через коллектор под давлением (до 500 кПа) подается исходная суспензия в пространство, ограниченное диафрагмой и фильтротканью. Фильтрат проходит через ткань и перфорированное днище в камеру фильтрата и отводится по коллектору, а твердые частицы оседают на ткань, образуя осадок.
По истечении определенного времени подачу суспензии прекращают и при необходимости осадок промывается водой и просушивается сжатым воздухом (под давлением 400–500 кПа), подаваемыми через коллектор 8. Для труднофильтруемых осадков в цикл фильтрования включается операция отжима влаги из осадка при помощи эластичной диафрагмы, расположенной над осадком. В полость над диафрагмой подается вода под давлением, диафрагма растягивается и выжимает воду из пор между частицами.
Плиты раздвигаются с образованием зазора и включается лентопротяжной механизм. Кек, образовавшийся на фильтроткани, при огибании ею направляющих роликов снимается ножами и сбрасывается на конвейер. Плиты снова уплотняются и цикл повторяется. Толщина кека может достигать 35 мм. Работа фильтр-пресса полностью автоматизирована. Период полного цикла фильтрования составляет 10–30 мин в зависимости от крупности фильтруемого материала и консистенции пульпы. Преимущества фильтр-прессов: значительная площадь фильтрования; возможность использования больших (до 2 МПа) перепадов давления на фильтровальной перегородке; минимальное содержание твердого в фильтрате; низкая влажность получаемых осадков – 7–8 до 10%.
К недостаткам фильтр-прессов следует отнести то, что они остаются значительно более сложными и дорогими аппаратами по сравнению с вакуум-фильтрами. На Среднеуральском медеплавильном заводе на фильтр-прессе ФПАКМ-25 при обезвоживании цинкового концентрата с содержанием твердого в питании 65% получен кек с влажностью 12%. В то время как на действующих дисковых вакуум-фильтрах ДУ 68-2,5 влажность осадка составляет 15,5–16,5%.
При фильтровании особо труднофильтруемых концентратов марганцевых шламов на фильтр-прессах по сравнению с вакуум-фильтрами получают осадок значительно меньшей влажности (до 26–28%).
Ремонт Рамные фильтр-прессы состоят из плит и заключенных между ними рам, плотно прижимаемых друг к другу нажимными плитами посредством электромеханического или гидравлического приводов. Фильтрующий материал (фильтровальная бумага) по периферии зажимается между обеими плоскостями плит и рамами. Исправная работа фильтра зависит от плотности в местах установки фильтрующей бумаги, целостности этой бумаги, точного совпадения осей отверстий в углах плит и рам, чистоты отверстий-каналов, соединяющих коллектор с камерами фильтрования и отверстий-каналов для спуска фильтрата. При ремонтных работах следует строго соблюдать эти условия. Поверхности сопряжения плит и рам должны быть хорошо обработаны и после монтажа строго параллельны друг другу; в противном случае невозможно гарантировать необходимую плотность. При очень сильном зажатии литые чугунные плиты и рамы могут поломаться.
Известны случаи коробления рам, такие рамы бракуют. Причиной поломки рам и плит могут быть неоднородность фильтровальной бумаги или складки на ней в местах сопряжения. Герметичность фильтрующих камер нарушается и тогда, когда давление в них превышает максимально допустимое из-за заполнения камер осадком. Поэтому во избежание аварий следует систематически проверять исправность клапана, отключающего систему при повышении давления. Отверстия-каналы в рамах и плитах проверяют щупом. Закупорка этих каналов часто служит причиной поломки плит под влиянием одностороннего давления.
Поверхности плит и рам постепенно изнашиваются, поэтому, если фильтруемая среда сильно агрессивна, поверхности покрывают свинцом или гуммируют, Все обнаруженные дефекты могут быть легко исправлены, поскольку для удаления осадка каждый раз приходится разбирать все плиты и рамы и часто менять фильтрующий материал. Поломанные плиты и рамы заменяют новыми. При ремонтах подвергают ревизии зажимное устройство. В случае электромеханического зажима вскрывают редуктор и проверяют состояние винта и гайки.
В случае гидравлического зажима проверяют поверхности плунжера и цилиндра, а также сальниковое уплотнение. Монтаж При монтаже, прежде всего, устанавливают на фундамент опорные плиты или стойки, проверяют их строгую горизонтальность и укрепляют фундаментными болтами. Затем устанавливают на соответствующие стойки упорную плиту и корпус зажимного механизма, которые соединяют опорными балками, закрепляемыми гайками. Особое внимание обращают на прямолинейность опорной балки (направляющей), которая может быть нарушена при транспортировании. После сборки опорная рама должна быть достаточно жесткой и не прогибаться под весом плит и рам. Зажимную плиту устанавливают ушками на направляющие опорных балок и подсоединяют к штоку зажимного устройства. Между упорной и зажимной плитами размещают необходимое количество чередующихся рам и плит, также опирающихся на опорные балки своими рожками.
Между соседними плитами и рамами ставят листы фильтровальной бумаги. Перед началом опрессовки под фильтр по всей его площади (между стойками) ставят противень из тонкого листа, а вдоль спускных краников (под ними) – приемный коллектор. Фильтр сдают после опрессовки и опробования зажимного механизма. Ремонт и монтаж вакуум-фильтра Монтаж Конструкция вакуумного фильтра, определяющая технологию монтажа и ремонта, зависит от характера движения фильтровальной перегородки и устройства распределительного механизма. Завод-изготовитель поставляет барабанный вакуум-фильтр отдельными узлами после контрольной сборки, регулировки и испытания.
На монтажной площадке для сборки фильтра, применяют самоходные или мостовые краны. Для проведения ремонтных работ обычно предусматриваются мостовые краны или кран-балки, поэтому до начала монтажа фильтров целесообразно смонтировать эти краны. Монтаж фильтра начинают с установки на фундамент нижнего корыта корпуса фильтра, несущего на себе всю нагрузку от барабана.
Корыто стропят за торцевые стенки и подвешивают к траверсе. По плоскости разъема корыто выверяют на строгую горизонтальность. Окончательная выверка производится после крепления фундаментных болтов. Трущиеся поверхности всех деталей и узлов очищают от консервационной (защитной) смазки, промывают керосином и просушивают. По обе стороны от корыта на фундаменте или раме размещают выносные подшипники так, чтобы после установки на них барабана была обеспечена строгая соосность барабана, корпуса и вкладышей подшипника. Со стороны привода устанавливают червячный редуктор, в корпус которого должна войти цапфа барабана с насаженным на его конец червячным колесом.
Редуктор окончательно фиксируют после проверки качества зацепления червячного колеса и червяка. Барабан поднимают только, с помощью траверсы, чтобы избежать искривления его оси и других повреждений. При установке на подшипники следует исключить возможность ударов, учитывая большие вес и габариты барабанов. От точности сборки сальников на выходе цапф из корпуса зависит плотность системы, поэтому корпус сальника крепят болтами к корыту после окончательной выверки оси барабана и устранения биения. Наибольшей точности требует сборка и регулировка распределительного (золотникового) устройства в соответствии со схемой распределения зон.
Пружины, прижимающие торец распределительной головки к диску цапфы, должны быть подтянуты равномерно, что позволяет избежать перекосов, а, следовательно, пропусков жидкости или подсоса воздуха. Сборку приводов барабана (электродвигателя с редуктором или вариатором) и шнека, крышки корпуса фильтра, а также трубопроводов производит в обычном порядке одна и та же бригада. Нож для съема осадка устанавливают так, чтобы по всей длине снимаемый слой был одинаковой толщины.
Собранный фильтр опрессовывается воздухом: корпус – на давление 1,1 кгс/см 2; барабан – на давление 1,25 кгс/см 2, коммуникации, соединяющие поверхность барабана с распределительным устройством, – на давление 1,7 кгс/см 2. Обтягивание барабана фильтровальной тканью – последняя операция перед пуском фильтра в эксплуатацию.
Эту операцию часто приходится выполнять также при эксплуатации и ремонте. Поверхность барабана обтягивают двумя слоями сетки: сначала крупной из легированной стальной проволоки, а затем мелкой из фосфористо-бронзовой проволоки. Первая сетка служит для отсасывания фильтрата или промывной жидкости, а также для подачи инертного газа; вторая сетка является основанием, на которое укладывают фильтрующий материал. Фильтрующая ткань натягивается на барабан и скрепляется в продольных и кольцевых пазах на поверхности барабана, выполненных в форме “ласточкина хвоста”. В пазах ткань удерживается чеканкой с помощью алюминиевой или свинцовой проволоки. Для плотного прилегания к поверхности барабана ткань прижимают к сетке барабана проволокой из бериллиевой бронзы диаметром 2 мм, спирально навиваемой по всей длине барабана. Равномерная укладка проволоки с достаточной затяжкой достигается применением специального намоточного устройства, которое перемещается вдоль вращающегося барабана фильтра винтом, вращаемым от самостоятельного привода.
Ремонт До начала ремонта освобожденный и промытый от продукта фильтр (включая корыто) тщательно продувают инертным газом. Ремонт фильтра зависит от характера неисправностей, обнаруженных при работе. Появление жидкости из вестовой трубы, проходящей через цапфу, свидетельствует о нарушении сварки корпуса барабана и внутренних соединительных трубопроводов. Для обнаружения дефектов и их ликвидации вскрывают корпус и опрессовывают сначала барабан, затем коммуникации. Дефекты легко обнаруживаются, если отдельные участки опрессовываемого воздухом барабана при вращении погружают в воду, которая заливается в нижнее корыто. Для внутреннего осмотра и ремонтных работ по торцам барабана открывают люки-лазы. Наиболее распространены следующие виды ремонтных работ: затяжка обмоточной проволоки, восстановление нарушенных участков чеканки фильтрующей ткани, набивки сальников по торцам корпуса, ремонт маслопроводов и лубрикаторов, подшипников шнека и редукторов.
Высокой квалификации требует ремонт распределительного устройства. Для обеспечения плотности прилегания золотника к планшайбе прибегают к шабровке с проверкой точности на плите. Имеющиеся риски и задиры предварительно должны сниматься проточкой поверхностей на станке. После сборки стаканы пружинящих прижимов проверяют на легкость вращения и отсутствие качки. Фильтры после монтажа, а также после ремонта подшипников, редукторов и некоторых других узлов обкатывают согласно инструкции сначала вхолостую, а затем под нагрузкой. Ремонт центрифуг Центрифугу останавливают на ремонт в соответствии с утвержденным годовым графиком осмотров и ремонтов.
При остановке центрифуги необходимо прекратить подачу суспензии, выключить электродвигатель, прекратить подачу воды, выключить электродвигатель насоса, очистить ротор, промыть. Каждый ремонт можно рассматривать как совокупность типового ремонта, объем и номенклатура работ которого предусматривается техническими условиями, и специальных ремонтных работ.
Такой подход позволяет выполнять подготовку к типовому ремонту в течение всего межремонтного периода, а в предремонтный период сосредоточить внимание на подготовке к выполнению специальных работ. При текущем ремонте осуществляют чистку барабана, регулировку зазора между корпусом барабана и ножами, набивку сальников, смазку подшипников шнека и замену масла в подшипниках барабана, проверяют центровку валов электродвигателя и редуктора. При капитальном ремонте кроме работ текущего ремонта производят замену сопла, ножей, манжет гидросистемы, пальцев и втулок муфты привода, подшипников барабана и редуктора привода, ревизию тормозов барабана с заменой тормозной ленты. Процесс ремонта центрифуги начинают с частичной разборки и наружной мойки. Затем разбирают центрифуги на агрегаты, агрегаты – на сборочные единицы, а последние – на детали, производят мойку деталей, контроль и сортировку деталей на годные, негодные и требующие ремонта. Изношенные детали ремонтируют.
Вместо негодных изготовляют новые либо берут из числа запасных. Из отремонтированных, годных и новых деталей подбирают комплекты. Из комплектов деталей собирают сборочные единицы и агрегаты, которые испытывают и затем окрашивают. Центрифугу собирают из сборочных единиц и агрегатов. После сборки центрифугу испытывают. Технологический процесс ремонта центрифуги заканчивают регулировочными работами, устранением дефектов, обнаруженных во время испытания, и окончательной окраской центрифуги. Монтаж центрифуг Завод-изготовитель поставляет центрифуги в полностью собранном виде или сборочными блоками, не требующими разборки при монтаже.
Современные промышленные центрифуги комплектуют виброизолирующими устройствами. Виброизолирующее устройство состоит из железобетонного постамента, шести пружинных подставок и четырех демпферов вязкого трения, предназначенных для гашения автоколебаний системы. Каждая пружинная подставка состоит из верхней и нижней опорных плит, двух цилиндрических витых пружин и стяжек. Центрифуги можно устанавливать на различных отметках производственных сооружений, так как виброизоляция практически полностью исключает передачу динамической нагрузки на строительные конструкции. Высоту помещения выбирают с таким расчетом, чтобы можно было произвести разборку и сборку машины, а на площадке вокруг нее можно было установить стеллажи для размещения демонтированных деталей и узлов. Монтаж центрифуги проводят в следующем порядке.
На подготовленную ровную и гладкую бетонированную площадку ставят пружинные подставки, предварительно сжатые с помощью стяжек в равной степени. На них устанавливают постамент, на который затем монтируют центрифугу и сборочные блоки. Между постаментом и бетонированным основанием ставят демпферы, которые верхним фланцем крепятся с помощью болтов к постаменту, а нижним – к основанию. Пружинные подставки удерживаются силой трения и не крепятся ни к основанию, ни к постаменту. Поверхность постамента перед установкой центрифуги необходимо промыть теплой водой; места, на которых обнаружены масляные пятна, тщательно вырубить; нижнюю поверхность станины центрифуги очистить от грязи, консервирующей смазки и промыть теплой водой. При установке центрифуги на постамент ее поднимают над уровнем постамента на высоту не менее 40 мм с помощью отжимных винтов, а также металлических пластин, входящих в монтажный комплект центрифуги, и выверяют по уровню. Допускаемое отклонение установки от горизонтальности равно 0,3 мм на 1 м.
Горизонтальность обеспечивается перемещением средних пружинных опор. После указанной подготовки основание центрифуги подливают бетонной смесью на высоту 100 – 120 мм. Подливку жидким бетоном рекомендуется начинать с одной стороны станины так, чтобы убедиться, что бетон проходит под всей поверхностью станины. Подливка должна производиться непрерывно. После того как бетон станет достаточно прочным, производят равномерную и окончательную затяжку фундаментных болтов и монтаж на постаменте привода, его ограждения, маслостанции и других съемных узлов и деталей, предварительно проведя их расконсервацию. При монтаже привода центрифуги необходимо обеспечить параллельность по осям и торцевым плоскостям приводных шкивов. Допускаемое отклонение – не более 1 мм.
Камерный Фильтр Пресс
Контроль натяжения ремней производят следующим образом: разделив межцентровое расстояние между шкивами примерно пополам, подвешивают на верхнюю ветвь ремня груз массой 5 кг; при этом провисание ремня не должно превышать 15 – 20 мм. При монтаже центрифуги все соединения трубопроводов и электропроводки должны быть эластичными. Это достигается установкой эластичных промежуточных элементов (металлических сильфонов, резиновых вставок и др.), обеспечивающих полную свободу перемещения в пределах от 10 до 20 мм. Ремонт трубопроводов В процессе эксплуатации трубопроводы изнашиваются от механического (в основном эрозионного), теплового и коррозионного воздействия. При ремонте выполняются следующие основные работы: 1) замена износившихся деталей и узлов или исправление их до соответствующих норм, допусков и размеров; 2) выверка трубопроводов, а в случае необходимости подгонка опор и подвесок; 3) модернизация или реконструкция трубопроводов с возможной унификацией сменных частей; 4) изоляция трубопроводов; 5) испытание на прочность и плотность; 6) окраска трубопроводов. За 2 – 3 ч до разборки фланцевых соединений трубопроводов резьбовую часть крепежных деталей необходимо смочить керосином.
Отворачивание гаек проводится в два приема: сначала все гайки ослабляются поворотом на 1/ 8 оборота, затем отворачиваются полностью в любой последовательности. При разборке трубопроводов с целью замены прокладок весьма трудоемка раздвижка фланцев. Для раздвижки фланцев используются специальные приспособления. Рисунок – Винтовое приспособление для раздвижки фланцев Рисунок – Приспособление для замены прокладки 1 – хомут; 2 – винт; 3 – болт. Для вырезки прокладок применяются специальные приспособления. Рисунок – Приспособление для вырезки прокладок 1 – конус; 2 – нож. При ремонте технологических трубопроводов изношенные участки заменяются новыми, дефектные сварные стыки удаляются, а вместо их ввариваются катушки.
Перед удалением участка трубопровода необходимо закрепить разделяемые участки так, чтобы предупредить их смещение. Участок, подлежащий удалению, крепится в двух местах.
После демонтажа участка трубопровода свободные концы оставшихся труб необходимо закрыть пробками или заглушками. При установке нового участка его сначала укрепляют на опорах, а затем сваривают. Сборка коллектора состоит из соединения отдельных участков, блоков (плетей), деталей и крепления его к опорам и подвескам. Отдельные узлы перед сборкой располагаются в цехе между аппаратами, насосами, арматурой.
Сначала сборка выполняется «начерно», т.е. Свариваемые детали соединяются прихваткой, фланцевые соединения собираются на монтажных болтах. После такой сборки и выверки горизонтальных и вертикальных участков осуществляется окончательная сварка стыков, а во фланцевых соединениях монтажные болты заменяются шпильками или постоянными болтами с окончательной их затяжкой.
После этого трубопровод закрепляется на опорах. Подъем и укладка узлов и деталей трубопроводов проводятся с помощью стационарных или передвижных грузоподъемных устройств.
При сборке отдельных участков трубопроводов передача их веса на насосы и компрессоры должна быть исключена. На вертикальных аппаратах заменяемые узлы и детали трубопроводов закрепляются стропами в двух местах для их подвешивания.
При подсоединении к другим узлам перестроповка исключается. Поднятый узел или деталь при помощи оправки подгоняется к присоединительному фланцу, а затем устанавливается прокладка и закрепляются все шпильки и болты. После проведения указанных операций стропы снимаются. Если новый узел трубопровода присоединяется на сварке, то стропы снимаются после приварки его первым швом.
При ремонте фланцевых соединений зеркало фланца, находившегося в эксплуатации, очищается от старой прокладки, следов коррозии и т.д. Перпендикулярность уплотнительной поверхности фланца к оси трубы проверяют при помощи специального приспособления.
Рисунок – Проверка перпендикулярности уплотнительной поверхности фланца к оси трубы При ремонте межцеховых трубопроводов замена изношенных участков надземных трубопроводов может выполняться потрубно. Возможна также сборка участков из секций, которые собирают и сваривают из отдельных труб и их элементов вблизи трассы или в трубозаготовительной мастерской. В условиях эстакад, насыщенных большим количеством трубопроводов, ремонт становится более сложным. В этом случае замена изношенных участков или прокладка дополнительных линий возможна лишь отдельными трубами небольшой длины. Трубы поднимаются краном или лебедкой и через верх или бок эстакады заводятся на место.
Сборка ведется в направлении, противоположном уклону трубопровода. При укладке трубопроводов на эстакадах, в каналах или лотках окончательное закрепление начинают с неподвижных опор. При замене участков трубопроводов, работающих при высокой температуре, а также при прокладке дополнительных линий проводится растяжка компенсаторов температурных удлинений. Растяжка компенсаторов осуществляется с помощью специальных приспособлений, вместе с которыми компенсатор монтируется. После закрепления концов трубопровода на неподвижных опорах приспособление удаляется. Рисунок – Винтовое приспособление для растяжки компенсаторов 1 – распорка; 2 – натяжная гайка; 3 – винт; 4 – хомут; 5 – труба.
Линзовые компенсаторы устанавливаются на трубопроводах, имеющих продольное и поперечное перемещения. Для предотвращения разрыва линз при сдвиге трубопровода в поперечном направлении на компенсаторах ставятся стяжки.
Линзовые компенсаторы растягиваются на половину их компенсирующей способности. Рисунок – Линзовые компенсаторы со стяжками 1 – тяга; 2 – лапа.
При ремонте трубопроводов, уложенных в грунт, выполняются следующие основные работы: 1) вскрытие засыпанных траншей; отсоединение участков трубопроводов; 2) подъем этих участков на поверхность; 3) очистка наружной поверхности от следов коррозии и остатков старой антикоррозионной изоляции; 4) замена изношенных участков трубопроводов новыми; 5) наложение новой изоляции; 6) укладка трубопровода в траншею. При наличии мелких повреждений (трещины, раковины, потения и т.д.) трубопровод из работы не выключается. При нетоксичных продуктах ремонт осуществляется наваркой заплат. Разрывы стыков и крупные трещины временно изолируются наложением хомутов.
Фильтр Пресс Инструкция
После освобождения трубопровода от продукта поврежденные места вырезаются и ввариваются катушки. Трубопроводы диаметром до 300 мм, уложенные на глубине не более 1,2 м, ремонтируются с подъемом и укладкой их над траншеей на лежаки. При диаметре более 300 мм ремонт осуществляется непосредственно в траншее с подъемом трубопроводов на высоту 60 – 70 см от дна траншеи с укладкой их на лежаки. Основным видом ремонта подземных трубопроводов является замена изношенного участка новым. При этом способе извлеченный из траншеи трубопровод разрезается на отдельные части и увозится на ремонтную базу. Новая секция вваривается в коллектор.
При подъеме и опускании трубопровода в траншею наиболее напряженные сварные стыки усиливают муфтами или планками. Для лучшего прилегания планок к трубопроводу в середине планок делается выгиб. При усилении муфтами их длина принимается равной 300 мм для труб диаметром 200 – 377 мм и 350 мм для труб диаметром 426 – 529 мм. Диаметр муфты принимается на 50 мм больше диаметра трубопровода. Толщина стенки муфты и трубопровода должна быть одинакова. Допускаемый зазор между муфтой и трубой составляет 2 мм. При ремонте иногда нужно подключиться к действующим трубопроводам соседних цехов.
Такая необходимость возникает и при подключении нового аппарата к действующим цеховым трубопроводам. Подобные врезки чаще всего осуществляются в период остановочных ремонтов.
Врезка в действующий трубопровод выполняется с использованием специального приспособления. К трубопроводу в месте врезки подгоняется и приваривается патрубок с фланцем. К этому фланцу на шпильках присоединяется задвижка требуемой серии. К задвижке на фланце крепится приспособление, состоящее из сверла и коронки, на которой укреплены резцы, шток, сальник, грундбукса, упорный шарикоподшипник и штурвал. Вращением коронки при помощи штурвала в стенке основного трубопровода вырезается отверстие требуемого диаметра. После этого шток с коронкой поднимается выше клинкета задвижки и последняя закрывается. Затем с задвижки снимается приспособление и к отводящему патрубку присоединяется новый трубопровод.
Рисунок – Приспособление для врезки отвода в действующий трубопровод 1 – трубопровод; 2 – сверло; 3 – резец; 4 – коронка; 5 – патрубок; 6,9 – фланцы; 7 – шток; 8 – задвижка; 10 – сальник; 11 – грундбукса; 12 – упорный шарикоподшипник; 13 – штурвал. После окончания капитального ремонта трубопроводов проводятся проверка качества работ, промывка или продувка, а затем испытание на прочность и плотность. Технологическая аппаратура перед испытанием отключается, концы трубопровода закрываются заглушками. Заглушаются все врезки для контрольно-измерительных приборов.
В наиболее низких точках ввариваются штуцеры с арматурой для спуска воды при гидравлическом испытании, а в наиболее высоких – воздушки для выпуска воздуха. В начальных и концевых точках трубопровода устанавливаются манометры с классом точности измерения не ниже 1,5. Гидравлическое испытание на прочность и плотность обычно проводится до покрытия тепловой и антикоррозионной изоляцией. Величина испытательного давления должна быть равна 1,25 максимального рабочего давления, но не менее 0,2 МПа для стальных, чугунных, винипластовых и полиэтиленовых трубопроводов. Давление при испытании выдерживается 5 мин.
После этого оно снижается до рабочего значения. Трубопровод тщательно осматривается. Сварные швы обстукиваются легким молотком. После проведения испытания открываются воздушки и трубопровод полностью освобождается от воды. Пневматическое испытание осуществляется воздухом или инертным газом. При этом выдерживается давление, равное 1,25 максимального рабочего давления, но не менее 0,2 МПа для трубопроводов из стали. Испытание на прочность чугунных и пластмассовых надземных трубопроводов не проводится.
Пневматическое испытание трубопроводов на прочность не проводится также в действующих цехах, на эстакадах, в каналах, т.е. Там, где находятся действующие трубопроводы.
Газопроводы, работающие при давлении до 0,1 МПа, испытывают давлением, которое устанавливается проектом. § 9.2 Ремонт трубопроводной арматуры Вся арматура, применяемая на химических и нефтеперерабатывающих заводах в системе технологических трубопроводов и на отдельных аппаратах, должна быть подвергнута периодической ревизии независимо от того, наблюдались ли в системе неисправности в процессе эксплуатации или она работала надежно. Многие вентили или задвижки на протяжении всего межремонтного пробега находятся в одном и том же положении (открыты или закрыты), поэтому при каждом ремонте арматуру следует “расходить”, пока маховик не начнет вращаться свободно, а шпиндель с запорным органом – подниматься и опускаться. Арматура, подвергаемая ревизии, не снимается с трубопровода, если в этом нет необходимости. Прежде всего, проверяют легкость открывания и закрывания задвижек, вентилей и кранов. Затем разбирают крышку, извлекают маховик вместе со штоком (шпинделем) и запорным органом (клином, плашками, клапаном или пробкой) и проверяют состояние уплотняющих поверхностей.
Если при эксплуатации проверяемой арматуры не были замечены пропуски, то достаточно визуального осмотра деталей и ее вновь собирают. В случае необходимости перебивают сальниковое уплотнение.
Окончательная затяжка сальника производится по мере вывода трубопровода на нормальный режим. Требующую ремонта арматуру демонтируют, промывают и в собранном виде отправляют в мастерскую. Здесь ее разбирают и путем осмотра и замеров устанавливают дефекты. Разборка производится в следующей последовательности: сначала снимают маховик (штурвал), затем разбирают крышку, извлекают шток вместе с запорным органом. При осмотре штока и запирающих поверхностей определяют характер ремонта.
Клин, плашку у задвижек и клапан у вентиля осматривают через лупу, а седла под них в корпусе арматуры (если они не видны) – с помощью зеркала или системы зеркал. Если на уплотнительных поверхностях имеются изношенные участки и раковины глубиной до 0,5 мм, их шлифуют; износ глубиной до 0,1 мм ликвидируется притиркой. В процессе притирки, т.е. Взаимного перемещения сопрягаемых деталей (или детали) и притира (плиты или оправки), в поверхность которых вдавлен абразивный материал, детали искусственно изнашиваются. Притиры изготавливают из мелкозернистого чугуна, их рабочая поверхность должна быть очень точной и чистой.
В качестве абразивного материала применяют наждачный, корундовый и кварцевый порошки, а также искусственные материалы (карбиды кремния и бора и др.). Большинство притирочных работ производят с помощью паст.
Распространена паста ГОИ (Государственного оптического института), содержащая окись хрома (74 – 81%), стеарин (10%), расщепленный жир (5 – 10%), силикагель (1,8 – 2%) и другие составляющие. Различают грубую, среднюю и тонкую пасты.
Тонкой пастой обычно завершают притирку уплотнительных поверхностей арматуры. До начала притирки притираемые поверхности тщательно промывают бензином или керосином и насухо вытирают чистой тряпкой. Абразивный материал, смешанный с маслом, или паста, разведенная в керосине, тонким слоем наносится на поверхность детали. Затем на эту поверхность накладывается притир или сопрягаемая деталь. Притираемые детали (или деталь и притир) взаимно перемещаются и одновременно легко прижимаются друг к другу.
Движения должны быть такими, чтобы поверхности притирались равномерно на всех участках. В процессе притирки порошок или пасту несколько раз меняют, каждый раз, тщательно удаляя предыдущий слой керосином. Притирку производят вручную или на специальных притирочных машинах. Качество притирки определяют “на карандаш” или “на краску”. Способ проверки “на карандаш” заключается в том, что на подготовленных поверхностях плашек, клина, клапана или пробки (для кранов) наносят тонкие поперечные риски. Если после сопряжения притираемых деталей и их взаимного перемещения риски везде окажутся стертыми, то считают, что достигнута хорошая притирка.
Разъединенные поверхности, покрытые многочисленными раковинами, восстановить притиркой невозможно. Такие поверхности обтачивают и шлифуют на станках.
При сильном износе поверхности клина, плашек, клапана, пробки и корпуса наплавляют для восстановления размеров и затем обрабатывают на станке. Привалочные поверхности фланцев корпуса и крышки также наплавляют и обрабатывают на станке. Сменные уплотнительные кольца в корпусе заменяют новыми. Отличительная особенность ремонта предохранительных клапанов – тщательная проверка пружин.
После разборки их промывают в керосине и осматривают. Пружины с забоинами, рисками и вмятинами на поверхности бракуются. Отклонение опорных плоскостей от перпендикулярности к оси пружины не должно быть более 0,01 ее высоты. Пружина не должна обладать остаточной деформацией; при проверке ее трехкратно сжимают статической нагрузкой. При ремонте каждого предохранительного клапана следует руководствоваться инструкцией, составленной для клапанов данной конструкции. Предохранительные клапаны регулируют и испытывают воздухом на специальном стенде. Клапан считается отрегулированным, если при заданном давлении он открывается, а при снижении давления закрывается с хлопком.
После ремонта арматура испытывается на прочность и плотность опрессовкой. Монтаж трубопроводов Монтаж трубопроводов выполняют узлами, секциями и блоками. В настоящее время получил распространение монтаж агрегатированными блоками, т.е. Блоки трубопроводов собирают вместе с технологическим оборудованием и устанавливают их на общую раму.
Укрупнительную сборку блоков выполняют на стендах и стеллажах, располагаемых в зоне действия монтажных кранов. Перед сборкой блоков с арматуры и узлов снимают временные заглушки и расконсервируют фланцы и концы труб. После контрольных замеров готовых узлов и проверки расположения штуцеров у оборудования начинают сборку блоков. Размеры и масса блоков должны обеспечивать удобство их транспортировки к месту монтажа и установки в проектное положение.
Узлы и блоки при подъеме должны сохранять прочность, в противном случае может произойти их деформация. При необходимости нужно устанавливать временные конструкции, обеспечивающие требуемую жесткость. Монтаж трубопроводов рекомендуется начинать с обвязки оборудования, т.е.
В первую очередь монтировать узлы и блоки, включающие в себя арматуру, а также базовые узлы с арматурой основных магистральных участков трубопроводов. Прямые участки прокладывают после монтажа и закрепления смежных узлов и блоков. На поднимаемых узлах и блоках целесообразно крепить опоры и подвески, это облегчает последующую выверку. При установке в проектное положение узлы и блоки, а также секции и отдельные трубы должны быть уложены не менее чем на две опоры и надежно закреплены. Трубопроводы, прокладываемые через стены, перекрытия или другие элементы зданий, должны заключаться в гильзы в соответствии с указаниями проекта.
При отсутствии указаний рекомендуется использовать в качестве гильз отрезки труб с внутренним диаметром на 10 – 20 мм больше наружного диаметра, заключенного в них участка трубопровода. Гильзы должны выступать на 50 – 100 мм с обеих сторон от пересекаемого трубопроводом элемента здания. Участки трубопроводов в гильзах не должны иметь стыков. Зазор между трубопроводом и гильзой заполняют с обеих сторон асбестом или другими негорючими материалами, допускающими перемещение трубопровода в гильзе.
Подъем и установка узлов и блоков в проектное положение осуществляются с помощью кранов, такелажного оборудования и устройств, предусмотренных проектом производства работ. Тали, блоки и другие такелажные средства, применяемые при монтаже трубопроводов, разрешается крепить к узлам строительных конструкций, обладающих необходимым запасом прочности. Трубопроводную арматуру устанавливают, как правило, в комплекте с узлами или блоками.
При монтаже арматуры, не вошедшей в состав узлов или блоков, ее предварительно закрепляют на опорах, после чего присоединяют к ней трубопровод. Монтаж наружных надземных трубопроводов целесообразно выполнять укрупненными блоками и секциями. Габариты и конструкции блоков или секций определяются проектом производства работ и зависят от конструкций эстакад, количества и расположения трубопроводов на эстакадах, их диаметров, наличия у монтажной организации грузоподъемных механизмов, а также условий монтажа. Укрупнительная сборка блоков и секций производится на стационарных или передвижных линиях. Секции поднимают на опоры или эстакады обычно с помощью двух кранов. Монтаж подземных трубопроводов выполняют в следующей последовательности: разрывают траншеи; подчищают дно и стенки траншей; роют приямки в местах сварки и изоляции стыков; устраивают основание под трубопровод; выполняют днища колодцев и камер; опускают трубы в траншеи, укладывая их на основание; собирают и сваривают замыкающие стыки; производят монтаж соединительных деталей и арматуры, подбивают и присыпают трубопровод грунтом (кроме стыков); продувают трубопровод воздухом; предварительно испытывают трубопровод на прочность; изолируют стыки; засыпают трубопровод.
Окончательное испытание трубопровода выполняют после окончания строительно-монтажных работ. Для центровки торцов труб, собираемых под сварку, и устранения несовпадения кромок по периметру труб применяют центраторы. Рисунок – Приспособление для центровки труб при сварке 1 – основание; 2 – опорная призма; 3 – прижимная призма; 4 – опора для винта; 5 – хомут; 6 – винт. Трубопроводы, укладываемые в траншеях, рекомендуется монтировать секциями и плетями длиной до 1000 м.
При этом готовые заизолированные трубы или секции длиной 24 – 36 мм раскладывают у бровки траншеи, собирают и сваривают их стыки в неповоротном положении. Сборку плетей производят на брусьях-лежаках или на вынутом грунте для удобства последующей их строповки при укладке в траншею. Между лежаками следует предусматривать расстояние до 35 м, дно траншеи планировать с учетом проектного уклона. Чтобы не повредить изоляцию, трубопровод поднимают с помощью специальных строповочных устройств – полотенец, состоящих из стального каната и внутренней защитной оболочки из прорезиненной ткани. Укладку плети в траншею рекомендуется выполнять с помощью трех кранов, расположенных вдоль плети на расстоянии 15 – 40 м друг от друга в зависимости от диаметра трубопроводов. СПИСОК ИСПОЛЬЗОВАННОЙ ЛИТЕРАТУРЫ 1.
Ермаков В.И., Шеин В.С. Ремонт и монтаж химического оборудования: Учебное пособие для вузов. – Л.: Химия, 1981. – 368 с., ил. Ермаков В.И., Шеин В.С. Ремонт и монтаж химического оборудования: Учебное пособие для вузов.
2-е изд., перераб. – М.: Машиностроение, 1992. – 208 с., ил. Фарамазов С.А. Ремонт и монтаж оборудования химических и нефтеперерабатывающих заводов. – М.: Химия, 1971. – 296 с., ил.
Рачмилевич З.З., Радзин И.М., Фарамазов С.А. Справочник механика химических и нефтехимических производств. М.: Химия, 1985. – 592 с., ил.
Гайдамак К.М., Тыркин Б.А. Монтаж оборудования предприятий химической и нефтехимической промышленности.
Учебное пособие для проф.-техн. Заведений и подгот. Рабочих на производстве. – М.: Высшая школа, 1974. – 286 с., ил. Маршев В.З., Петрухин И.П. Монтаж оборудования предприятий химической и нефтяной промышленности: Учебное пособие для ПТУ.
– М.: Высшая школа, 1990. – 208 с., ил. Персион А.А., Гарус К.А., Монтаж трубопроводов. Справочник рабочего. – К.: Будiвельник, 1987.
– 208 с., ил. Лукьяненко В.М., Таранец А.В. Центрифуги: Справ. – М.: Химия, 1988. – 384 с., ил.